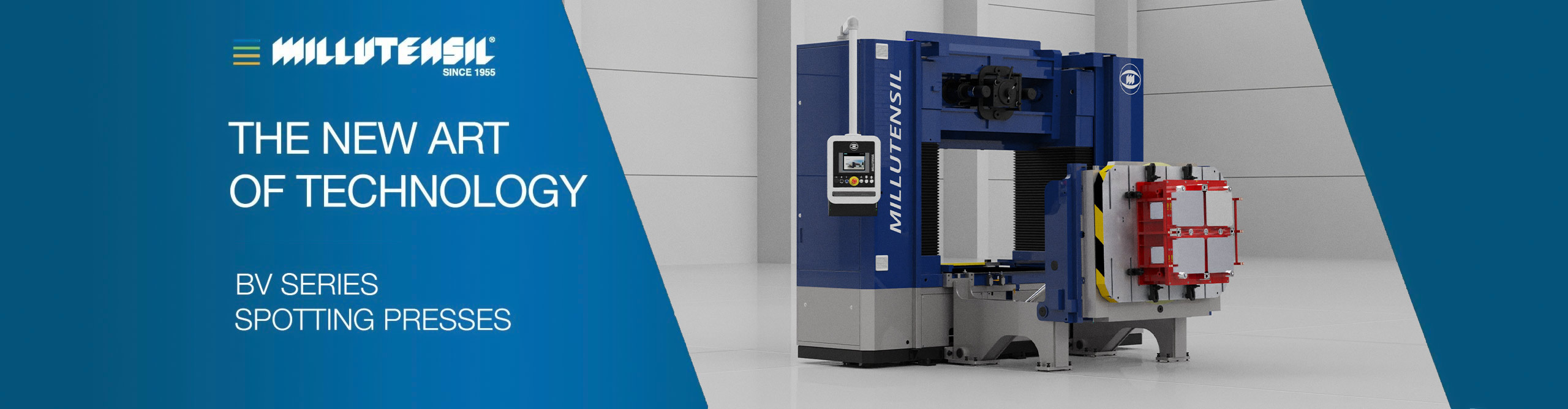
SPOTTING PRESSES FOR ASSEMBLY, ADJUSTMENT, CHECKING AND REPAIR OF SMALL AND MEDIUM MOULDS AND DIES
BV E SERIES
The press is used for splitting, adjusting, maintenance and try-out operations on dies and moulds (thermoplastics, die casting, thermosetting, rubber and blanking).
The BV series is suitable for small and medium-sized moulds. Three models are available depending on the platen dimensions: BV 26E, BV 28E and BV 30E. Platen dimensions are available from 980 ×750 mm up to 1500×1000 mm. The very sturdy structure consists of a welded and normalized steel basement and cast iron baseplate. Hydraulic system is controlled by electronic servo proportional valves.
All E models are equipped with user-friendly graphics control panel, monitored through Siemens PLC commanded by Touch Panel installed in the pulpit station.
All components are purchased from well-known manufacturers, such as for example: hydraulic system Bosch-Rexroth, Hawe; electrical system Siemens, Schneider Elektrik, Phoenix Contact, Weidmüller. This guarantees a general good functionality of the press, and a quick procurement all over the world.
EC Declaration of Conformity and compliance with safety provisions in accordance with the current EC standards.
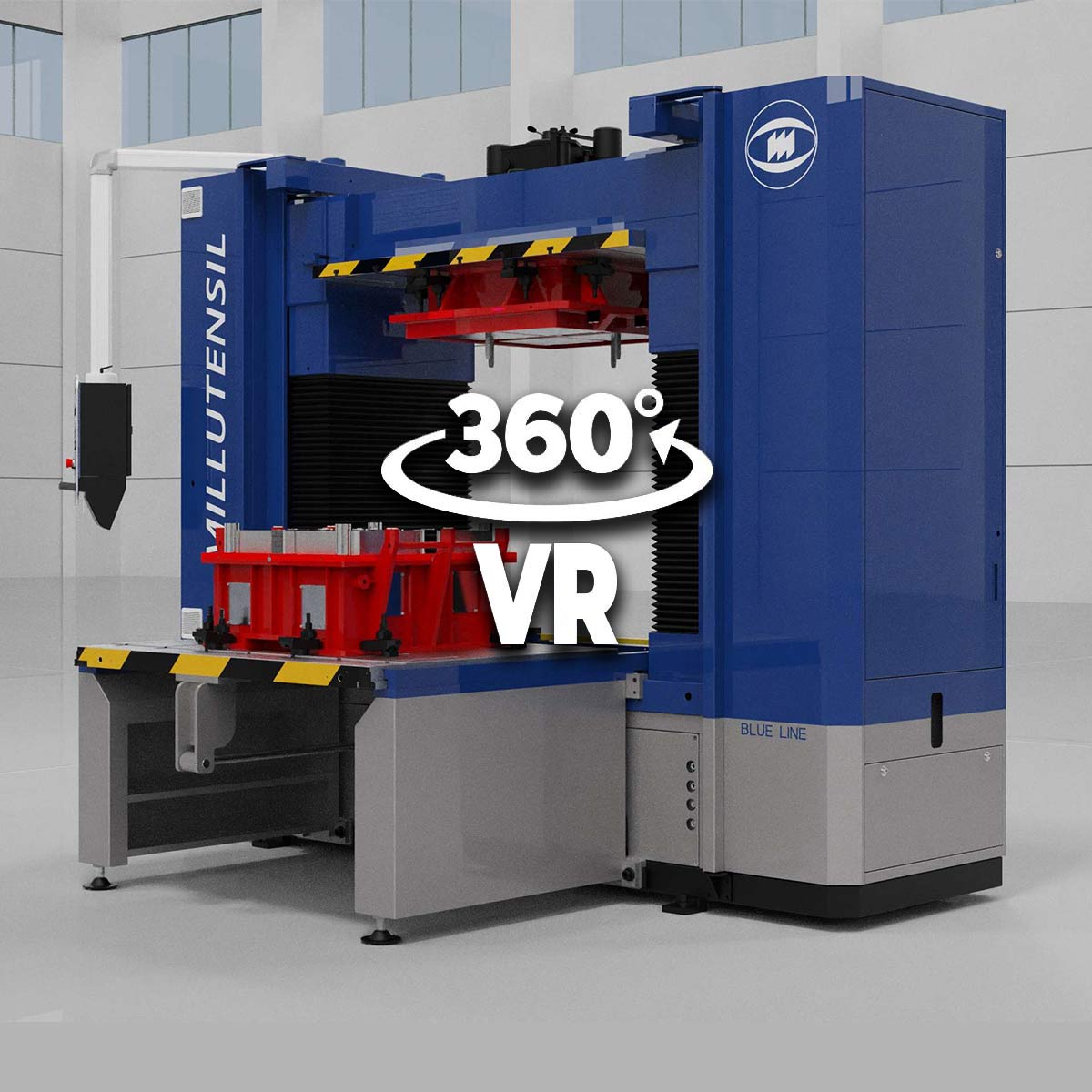
BV26E – Platens dimension: 980×750 mm
BV28E – Platens dimension: 1.200×1.000 mm
BV30E – Platens dimension:: 1.500×1.000 mm
STANDARD MOVEMENTS OF THE PLATENS
The upper plate slides vertically by hydraulic actuation on the four guide columns and can be overturned 360° through reduction gears. The upper plate clamping in the exact horizontal position depends on the four hydraulic actuated locating pegs.
The lower plate is hydraulically extensible, sliding on the base guided by ball bearings. It allows to draw the lower part of the die or mould out of the press into an effortless working position.
All functions are comfortably performed from the touch panel.
STANDARD MOVEMENTS OF THE PLATENS
The upper plate slides vertically by hydraulic actuation on the four guide columns and can be overturned 360° through reduction gears. The upper plate clamping in the exact horizontal position depends on the four hydraulic actuated locating pegs.
The lower plate is hydraulically extensible, sliding on the base guided by ball bearings. It allows to draw the lower part of the die or mould out of the press into an effortless working position.
All functions are comfortably performed from the touch panel.
VIDEO
FEATURES
Structure
- Press with 4 chrome-plated alloy steel columns, structures made of welded and normalized steel, nd a sturdy cast iron baseplate to guarantee high rigidity and bending resistance.
- Basement embedded in a robust arc-welded structure, that is highly rigid and flexion-proof
- 2 hydraulic cylinders for the upper plate actuation guarantee an optimal distribution of surface pressure.
- Easy clamping force setting, by means of the touch panel.
- Room-saving arrangement of the hydraulic power unit with considerable noise reduction in press upper part.
- The hydraulic power unit can be easily and safely reached by means of a specific ladder.
- Very long maintenance-free press ram precision guides, with bronze bushings lubricated for life with teflon coating
CONTROL PANEL
TOUCH PANEL FOR BV-E SERIES
Millutensil was the first worldwide to introduce a TOUCH PANEL on its spotting presses. The electronic PLC handles all the functions of the press (BV-E series). Uncluttered, clear and ergonomic, the panel offers many advantages as well as vast flexibility in customizing features, including command of the auxiliary cylinders.
Siemens S7-1500 control easy to program and use.
The pulpit station is equipped with a touch panel with a user-friendly graphics to simplify the use of the spotting press. All working movements and functions are graphically shown on the display.
Two-hands command.
Due to security reasons, some functions can be activated only through traditional buttons (i.e. downstroke must be carried out with two-hands, in compliance with EU-UL-CSA safety legislation).
In the pulpit station a new Siemens multi-touch ITP 1000 can be embedded (OPTIONAL).
This new Siemens multi-touch ITP 1000 is supported by a dedicated app called MyMILL© App, that has been developed by Millutensil as a result of the ongoing cooperation between Millutensil and their customers.
speed control and setting
The upper plate CLOSURE/OPENING speeds can change automatically thanks to a particular system developed by Millutensil and defined in LEVELS (L1, L2,L3).
The setting of levels (L1, L2,L3) considerably facilitates adjusting operations.
The advantages are:
- maximum repeatability and safety of movements;
- reduction of the risk of accidental impacts.
After fixing the mould, the operator can set, as he deems fit, two different levels according to which the press will automatically apply the corresponding speed changes (L1, L2).
These levels will remain stored can be applied during all opening and closing operations.
The maximum pressure set will be reached in L3 only, when the mould is completely closed.
Operator panel for the setting of levels:
Thanks to this modern system, it is possible to set several speeds (fast during the approaching phase, medium during the working phase and slow during the final mould closing phase).

OPTIONAL VERSIONS

OPTION -R
Lower plate tilting by 90°
Thanks to 2 hydraulic cylinders, the lower plate can be tilted up to 90°, on the short back side, to operate on the mould at an ergonomically better position.
Tilting movements (and automatic locking) are controlled by the touch panel.
The plate can be placed at any angle, giving the operator optimal access to the mould, with no need to bend, maximum comfort and safety.
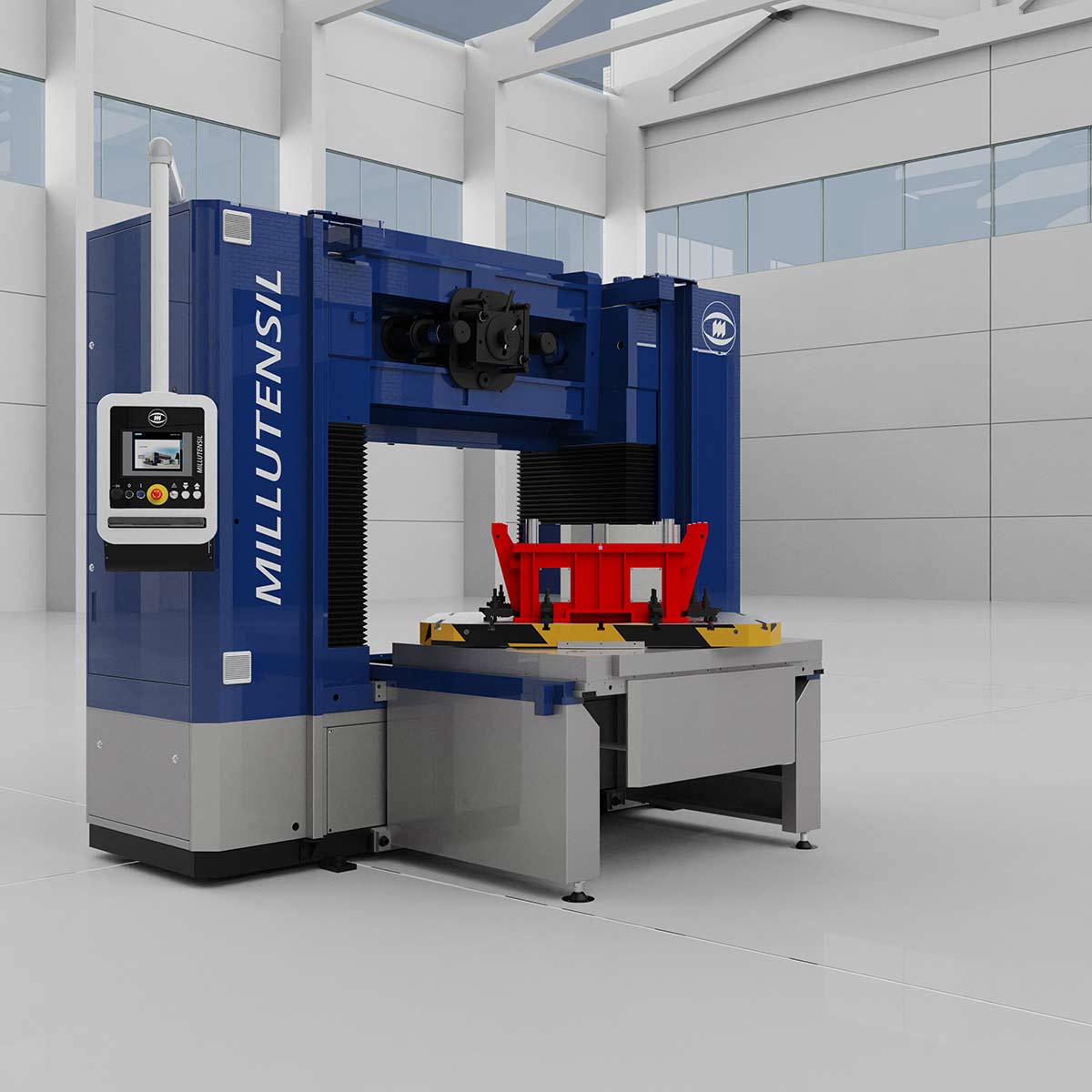
OPTION -G
Extensible plate with integrated 0-180° or 0-90°-120°-180°-240°-270° rotating table for multi-component moulds.
The integrated rotating table in the press’ lower plate has been designed to facilitate themulti-component mould adjustment. Time and cost savings are guaranteed, as moulds do not need to be manually rotated in order to be tested, which is very time consuming.
Furthermore, there is a significant ergonomic gain as the mould can be placed in many different angles, so that the operator who can position the lower half-mould in an optimal and comfortable position to carry out adjusting.
The rotating function is comfortably performed from the touch panel.Press plate rotation is possible either in the 0°-180° or in the 0°90°-120°-180°-240°-270° positions.

OPTION -RG
Extensible plate tilting by 90° with integrated 0-180° or 0°-90°-120°-180°-240°270° rotating table.
The combination of the optional extensible plate 90° tilting devices with the integrated rotating table (0°-180 or 0°-90°-120°-240°-270°) guarantees an even higher operator’s ergonomics.
These combined devices make the spotting of multi-component and/or multi-colour moulds even easier.
EQUIPMENTS FOR THE PRESS
parallelism control system of platens
Electronic upper plate parallelism anti-unbalance safety device, protection of press and moulds.
The upper plate up/down stroke is based on a fully electronic management of the main hydraulic system, which through special proportional servo-valves controls and manages, with maximum accuracy, the oil flow generating the parallel movement of the 2 up/down stroke cylinders.
The control system includes measurement devices (Balluff absolute linear Encoder with magnetic codification), which continuously check the press upper plate position and parallelism compared to the lower plate, and which are located on the sides outside the upper plate, where columns are.
The value is dynamically displayed on the touch panel for the entire stroke.
If the preset limit parameters are exceeded, the ram closing movement is immediately disabled and the parallelism condition is automatically restored by means of the up stroke function. Parameters can be exceeded for example because of slides or hydraulic cylinders not retracted, or tools forgot in the mould (scrapers, grinders, slip gauges, hammers etc.).
Thanks to this system, both press and moulds are protected from potential damages.
Only high-end mold spotting presses are equipped with this system.
green mode
By means of a special low-pressure circuit, oil is sucked from the tank. This allows a higher speed, without heating the oil, with a definitively low energy consumption.
After 100 seconds out of service, the hydraulic unit turns off in order to save energy. By pressing the specific push-button, the group is activated and hydraulic pressure is immediately restored.
OPTIONAL EQUIPMENTS FOR THE MOULDS
Hydraulic ejection unit
Hydraulic ejector cylinder in the lower plate (option)
The ejection unit initiates the movement of the ejection pins of dies and moulds for plastic materials and die casting.
This utility is made up of a hydraulic cylinder located in the middle of the press basement.
It allows to check and test some important mould functions in a very short time.
The pressure / thrust force is set by means of the il touch panel. The operating pressure depends directly on the line pressure. The advantage is the sensitive test of the mould ejection systems.
ENERGY ACCUMULATOR
Patented single shot energy accumulator
This optional device is indispensable to set up dies and moulds for plastic materials and die casting. This exclusive Millutensil accessory is made up of two mechanical devices with hydraulic start-up assembled on the upper plate of the press.
Compression springs are loaded by means of hydraulic pressure. Their dynamic action creates micro-vibrations that, applied at the same time with the press clamping force, increases the efficiency of the Prussian blue marking. The advantage of using the single shot energy accumulator is that the final trail on the mould is straightforward as the surface sections to be improved are clearly displayed. Not to mention that production- and manual adjustment costs are also cut.
This system is applied at the end of the die & mould spotting process with the highest possible pressure. It acts on the closed mould without causing any inconvenient to it and to the press structures.
The dynamic action of this device is independent from the press clamping movement. As a consequence, the dynamic action of the energy accumulator will be coupled with the press clamping force.
Automatic special wax injection unit
The final mould quality trial can be performed by a low-pressure wax injection. It provides a way to inject special wax at a low pressure into the mould cavity.
In this way, mould makers can check dimensions and thicknesses of pre-production mouldings (even the thinnest flash) to ensure the correct filling. The wax injection unit includes: wax container with electric heating, pneumatic action with air pressure control and temperature control of the chamber to attain constant wax fluidity.
The injection unit is easy to access as it is placed on top of the ram. The electric heating temperature is set through a knob and adjusted with a thermostat.
For an easy mounting, the device can be moved transversally and longitudinally, and then fastened.
The injection function is activated directly on the touch panel. Injection is performed using compressed air with an operating pressure equal to Max 6 bar. Usually the wax has a recede factor of 0,6% and it can be used up to 4/5 times.
Upon request customized injector can be tailor designed with 20 bars Max pressure with disposable wax. On the display panel the injection timing is displayed. The use of hot channel systems excludes the use of the wax injection unit.
HYDRAULIC AUXILIARY CYLINDER CONTROL UNIT (MAX. 2+2)
The trial on slide’ and hydraulic cylinders’ movement is wholly integrated in the press. Through the touch panel it is possible to manage 2 pairs of hydraulic cylinders (2 inputs and 2 outputs), either individually or synchronously.
The operating pressure is variable, and it is set always on the touch panel. The hydraulic line connection is made using quick couplers and flexible hoses.
Upon customer’s request, it is possible to configure the mould’s marks with the spotting press in order to test the correct functioning of the sensors and of the hydraulic cylinders.
Hydraulic power unit
Separate hydraulic power unit on trolley with connections for hydraulic cylinders (4+4) (option)
A separate and standalone hydraulic power unit on trolley has been designed, in order to test the movements of slides and hydraulic cylinders. This trolley is equipped with a tank, and it is directly connected to the press control panel, with which it is possible to settle up to 4 pairs of hydraulic cylinders (4 inputs and 4 outputs), either individually or synchronously. Each connection pair is equipped with a standalone pressure regulator and an analogue pressure gauge.
The trolley can be provided in a completely stand-alone version with its own dedicated control panel, so that it can be used not only with the spotting press.
Upon the customer’s request, it is possible to configure the marks of the moulds with the spotting press, in order to test the correct functioning of the sensors and of the hydraulic cylinders. We can supply special cycles for the movement of slides/hydraulic cylinders.
The standard trolley is equipped with a pump with a delivery of 8 Liters/min. and a 2.2 kW engine. A customized trolley version is characterized by a pump with a delivery of 40 liters/min. and 11/15 kW engine. A special version for operation with water-glycol mix is also available.
TECHNICAL ASSISTANCE
Diagnostic system
Integrated diagnostic system
MILLUTENSIL die & mould spotting presses are equipped with a specific and exclusive diagnostic program. Any failures occurred during operations is displayed on the control display, where the affected point is indicated. As a consequence, the machine downtime is minimized.
Main advantages:
- Minimization of down time,
- Quick and easy troubleshooting,
- Considerable service costs reduction, especially after the warranty period.
E-Won modem
MIL-Series spotting presses are equipped with a E-Won modem, so that our Millutensil technicians can remotely operate on the spotting press to fix it.
The remote assistance can be easily performed thanks to the hotspot of a mobile phone and a password that is provided in case of need.
Wireless mobile panel
Thanks to the tablet Siemens multitouch ITP 1000 (optional) and its MyMILL© App (optional), remote assistance is simplified, since the tablet can be used to initiate the remote assistance call.
Training
For a complete use of the machine, we provide support and training to technicians during installation on site.
TECHNICAL DATA
Other solutions
BV 25P
perfect for small sized moulds.
The BV 25 P is the smallest and most simplified version of the Millutensil’s spotting presses, without hydraulic electronic and parallelism control.
The control panel of the BV 26 C is equipped with manual function buttons to simplify the use of the spotting press.
Platen dimensions are 770×660 mm.
BV 26C
perfect for small sized moulds.
The BV 26 C is the entry level version of the Millutensil’s spotting presses, without hydraulic electronic and parallelism control.
The control panel of the BV 26 C is equipped with manual function buttons to simplify the use of the spotting press.
Platen dimensions are 980×750 mm.
BV 32E – 33E – 34 – 35 E
perfect for medium sized moulds.
The BV 32E – 33E – 34 and 35 E are the advanced version with a hydraulic system controlled by electronic servo proportional valves and a control of parallelism through two specific linear encoders.
All models are equipped with user-friendly graphics touch control panel
Platen dimensions are 1.600×1.300mm or 2.000×1.500 mm.
As all E series, the BV 32/33/34/35 E series presses are offered with option -R, -G or -RG version and can also be equipped with all optional accessories.
Our worldwide references
