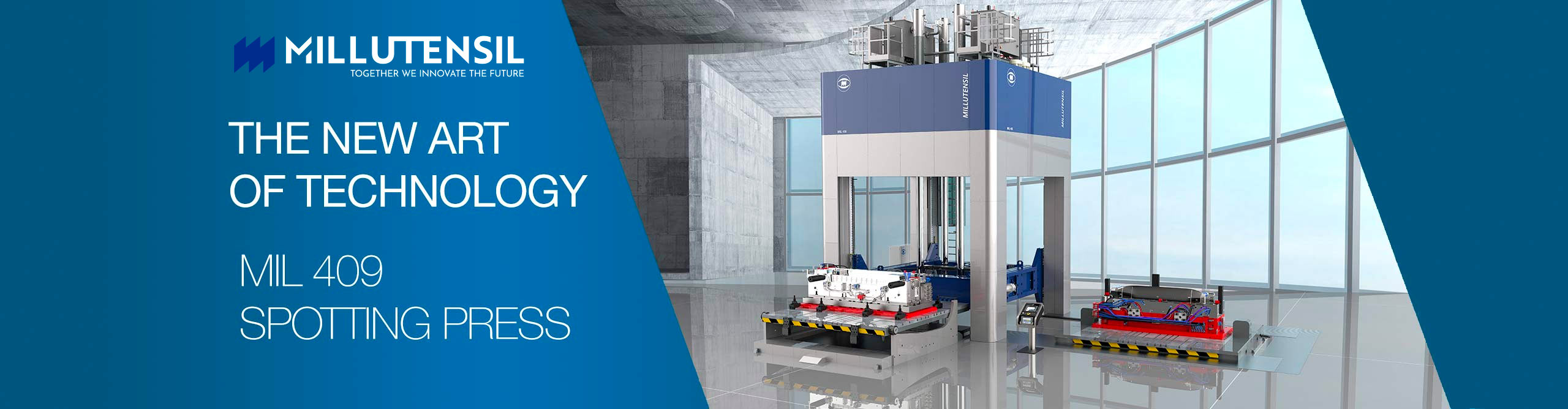
SPOTTING PRESSES FOR ASSEMBLY, ADJUSTMENT, CHECKING AND REPAIR OF GIGA DIES
MIL 409
The press is used for splitting, adjusting, maintenance and try-out operations on dies and moulds (thermoplastics, die casting, thermosetting, rubber and blanking).
Millutensil MIL 409 is the biggest and most powerful spotting press on the market.
Approximatly 11 meters high (8.5 over ground), it is equipped with a 4 x 4 meters plate, with a load capacity of up to 130,000 Kilograms on the lower plate, and 60,000 Kilograms on the upper plate, tilting up to 180°.
The MIL/CLASSIC series provides great advantages compared to other solutions with long side tilting:
- Better working ergonomics, granting the operator an easy access to any mould part, without the use of platforms;
- Much shorter total press height above ground, which often reduces excess costs for foundations;
- Wide base press structure with greater stability;
- The two mould-halves are located on the same side. In this way, operators have an overview of the whole mould and can work more comfortably.
All components are purchased from well-known manufacturers, such as for example: hydraulic system Bosch-Rexroth, Hawe; electrical system Siemens, Schneider Elektrik, Phoenix Contact, Weidmüller. This guarantees a general good functionality of the press, and a quick procurement all over the world.
EC Declaration of Conformity and compliance with safety provisions in accordance with the current EC standards.
PLATENS MOVEMENTS
LOWER PLATE
The lower plate is extensible, sliding on the base guided by ball bearings.
In the final position, the plate comes down and is held by means of 6 motor cylinders, thus completely leaning on specific ground support bands.
The system guarantees high repeatability accuracy equal to ± 0,04 mm.
It allows to draw the lower part of the die or mould out of the press into an effortless working position
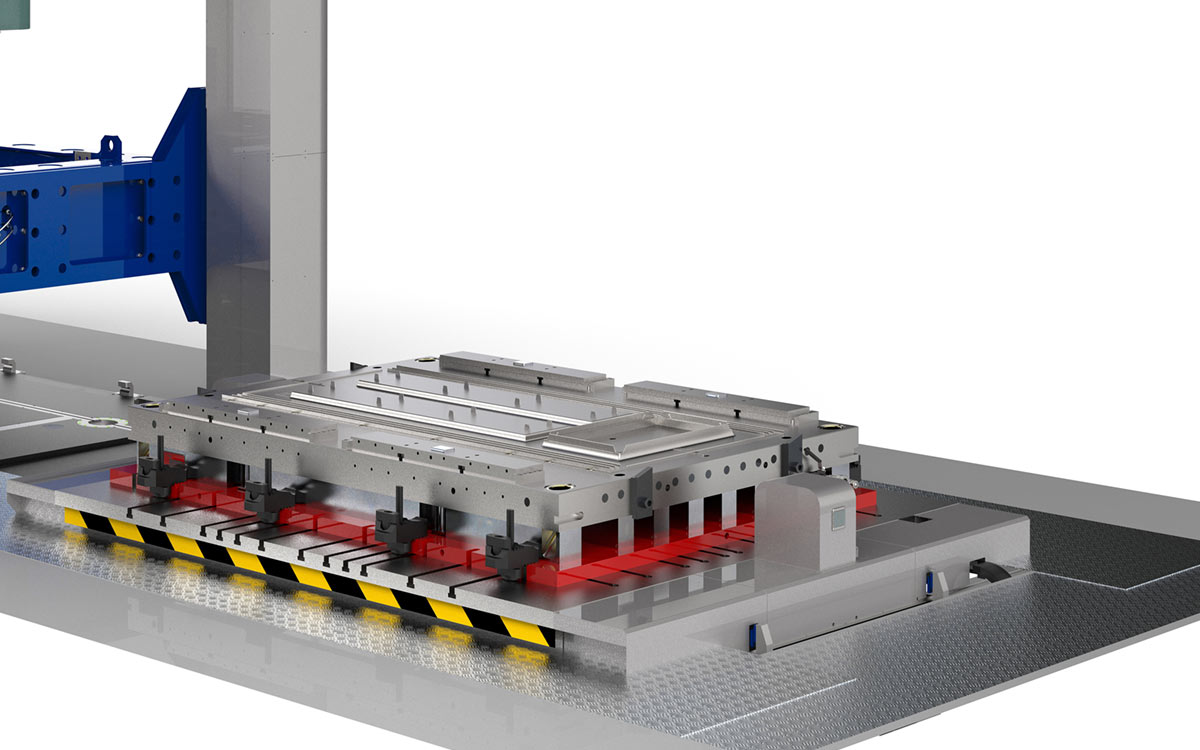
UPPER PLATE
In order to increase comfort and improve access to the press upper plate and to the moulds fastened on it, the upper plate can be tilted by up to ~180° downwards.
This occurs through the down stroke function with the plate leaning on 2 shaped brackets.
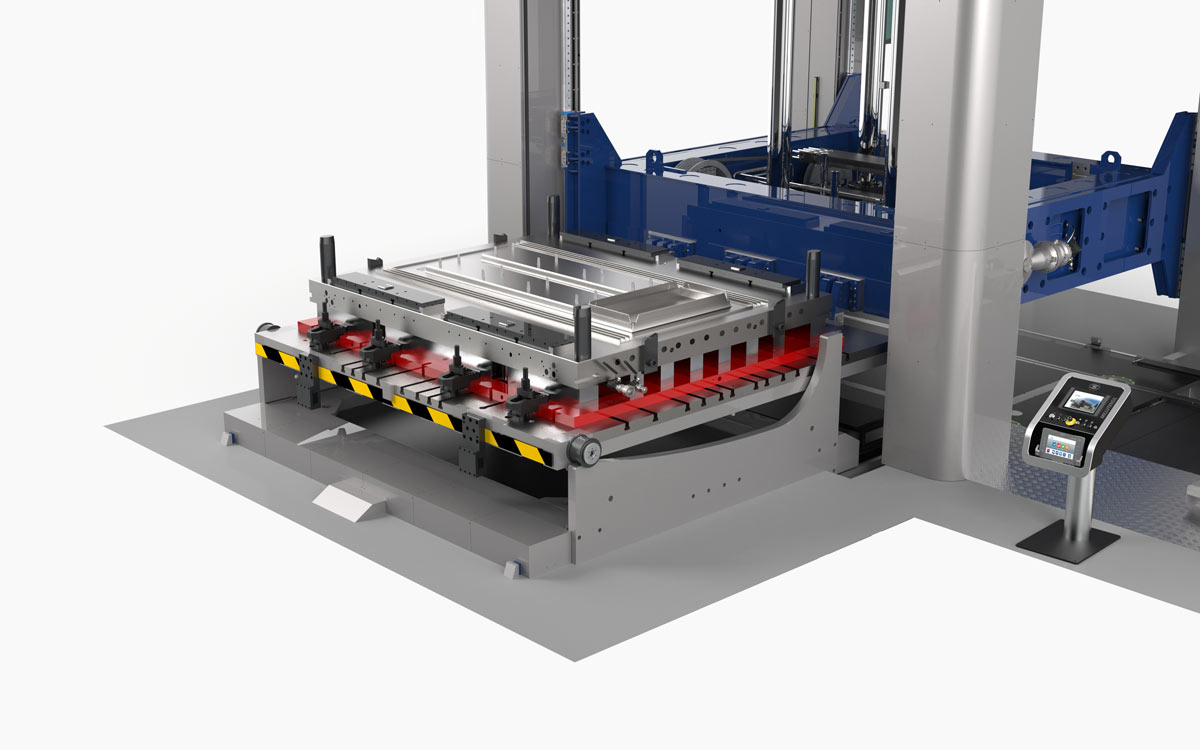
Elevating precision: MILLUTENSIL’s exclusive integrated system
MILLUTENSIL has pioneered a groundbreaking solution to address the increasing dimensions and weights of GIGA molds, which have become unmanageable using conventional technologies. MILLUTENSIL has developed a new and exclusive technology capable of maneuvering and tilting the upper half of the mold by 180 degrees. These molds can now reach dimensions of up to 4×4 meters and weigh a staggering 60000 kg.
This innovative technology relies on a sophisticated control system that utilizes two electric motors winches and two sliding side shelves with shaped brackets. and cables to manipulate the upper plate.
The synchronized movement of support shelves ensures the precise tilting of the upper plane up to 180 degrees, all while maintaining maximum accuracy and preventing any potential deformations.
Millutensil’s cutting-edge approach marks a significant advancement in handling large-scale molds, providing a solution that combines precision and stability in the face of unprecedented dimensions and weights.
- During the first phase the two side shelves slide centrally until they are positioned under the upper plate.
- Then, the upper press plate, supported on one side by two ropes driven by two electric motors winches and hinged on the opposite side of the intermediate block, is simply released and tilted by the gravity force, up to reach the balance of the center of gravity of the mould at about 60 °.
- The down stroke movement of the intermediate block allows the upper plate to be placed on the shaped brackets.
- Next, the combined action of the exit of the side shelves to the original position and the down stroke movement of the intermediate block, drags the upper plate to the final ~180° tilted position.
After complete closure, the press plate is automatically centred with high precision and locked by a system driven by hydraulic cylinders.
The use of plate tilting by up to ~180° guarantees optimal access and high working comfort in any working position.
VIDEO
FEATURES
HYDRAULICS
The hydraulic system is manufactured with components by the main international companies such as BOSCH, REXROTH, HAWE etc. in order to guarantee:
- high performance
- long operating life
- easiness to find spare parts all over the world
Green mode
Use of the gravity principle during the entire down stroke.
By means of a special low-pressure circuit, oil is sucked from the tank. This allows a higher speed, without heating the oil, with a definitively low energy consumption.
After 100 seconds out of service, the hydraulic unit turns off in order to save energy. By pressing the specific push-button, the group is activated and hydraulic pressure is immediately restored.
Energy-efficient and low-consumption LED lamps for the optimal lighting of the working area.
Hydraulic component layout
In the entire range of Millutensil die & mould spotting presses, the main hydraulic power unit is placed directly in the press upper part, and can be reached by means of a service ladder. The advantage is that there are no bulky tanks with noisy hydraulic power units located on the ground around the machine. This allows to reduce cable and pipe connections.
Moreover, the extensive press housing considerably facilitates cleaning and routine maintenance.
The upper platform, completely surrounded by specific protection panels, which is a particular design by Millutensil, also guarantees further noise abatement for motor/pump units.
CONTROL PANEL
Siemens S7-1500 control easy to program and use
Pushbutton station equipped with modern Siemens TP1200 MULTIPANEL TOUCH PANEL.
The pulpit station is equipped with a touch panel with a user-friendly graphics to simplify the use of the spotting press. All working movements and functions are graphically shown on the display.
Two-hands command.
Due to security reasons, some functions can be activated only through traditional buttons (i.e. downstroke must be carried out with two-hands, in compliance with EU-UL-CSA safety legislation).
Uncluttered, clear and ergonomic, the panel offers many advantages as well as vast flexibility in customizing features, including command of the auxiliary cylinders.
In the pulpit station a new Siemens multi-touch ITP 1000 can be embedded (OPTIONAL).
This new Siemens multi-touch ITP 1000 is supported by a dedicated app called MyMILL© App, that has been developed by Millutensil as a result of the ongoing cooperation between Millutensil and their customers.
speed control and setting
The upper plate CLOSURE/OPENING speeds can change automatically thanks to a particular system developed by Millutensil and defined in LEVELS (L1, L2, L3).
The setting of levels (L1, L2, L3) considerably facilitates adjusting operations.
The advantages are:
- maximum repeatability and safety of movements;
- reduction of the risk of accidental impacts.
After fixing the mould, the operator can set, as he deems fit, three different levels according to which the press will automatically apply the corresponding speed changes (L1, L2, L3).
These levels will remain stored can be applied during all opening and closing operations.
The maximum pressure set will be reached in L1 only, when the mould is completely closed.
Operator panel for the setting of levels:
Thanks to this modern system, it is possible to set several speeds (fast during the approaching phase, medium during the working phase and slow during the final mould closing phase).

EQUIPMENTS FOR THE PRESS
parallelism control system of platens
Electronic upper plate parallelism anti-unbalance safety device, protection of press and moulds.
The control system is made of 4 linear magnetic encoders with decimal precision, located on the external corners of the upper plate, near the columns.
They consist of an aluminium profile with an IO-Link language and a magnet for reading the position that runs close to the profile, without touching it.
This device is used to continuously check the position and the parallelism of the upper plate of the press compared to the lower plate.
The values measured are dynamically displayed on the touch panel for the entire stroke.
In addition to parallelism control, the entire functioning of our solution relies on the accuracy of the lower plate block thanks to hydraulic half cylinders that precisely fix the entire bottom plate allowing a perfect alignment of the two halves of the mold.
Thanks to this system, both press and moulds are protected from potential damages.
SAFETY
LIGHT CURTAINS: ACCIDENT-PREVENTION PROTECTION DEVICES
The spotting press is equipped with special safety devices made of optics immaterial barriers operated by a specific safety module controlled from the PLC. They are located in the rear area and on the opposite side to the extensible plate.
They guarantee maximum safety for areas partially out of sight of the operator.
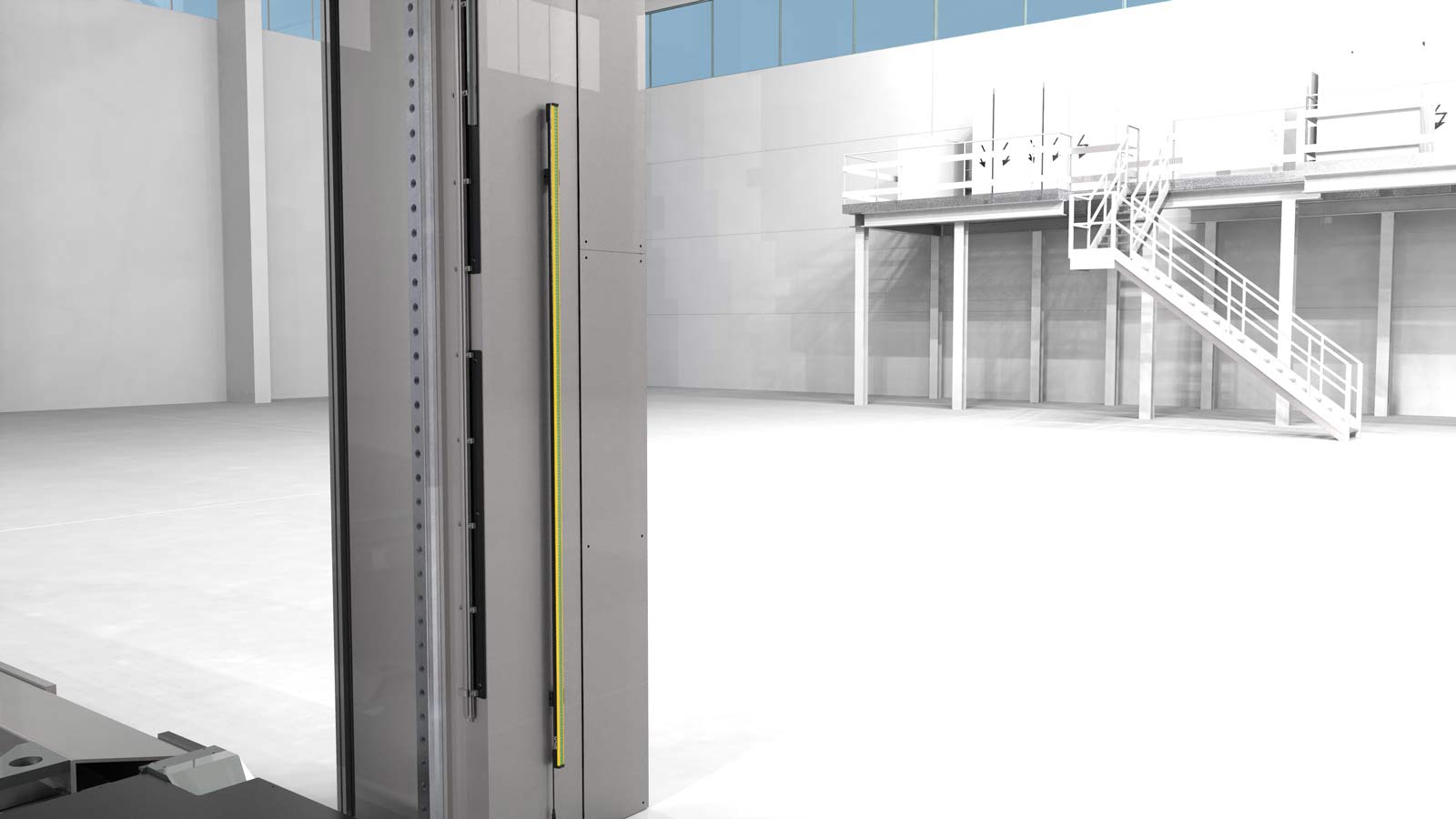
OTHER FEATURES
- Optimal arrangement of T slots for the mold clamping in both press plates.
- Centering holes in the lower and upper plates for the use of mould centering rings.
- Easy clamping force setting, by means of the touch panel.
OPTIONAL EQUIPMENTS FOR THE MOULDS
Hydraulic ejection unit
Hydraulic ejector cylinder in the lower plate (option)
The ejection unit initiates the movement of the ejection pins of dies and moulds for plastic materials and die casting.
This utility is made up of a hydraulic cylinder located in the middle of the press basement.
It allows to check and test some important mould functions in a very short time.
The pressure / thrust force is set by means of the il touch panel. The operating pressure depends directly on the line pressure. The advantage is the sensitive test of the mould ejection systems.
Hydraulic power unit
Separate hydraulic power unit on trolley with connections for hydraulic cylinders (4+4) (option)
A separate and standalone hydraulic power unit on trolley has been designed, in order to test the movements of slides and hydraulic cylinders. This trolley is equipped with a tank, and it is directly connected to the press control panel, with which it is possible to settle up to 4 pairs of hydraulic cylinders (4 inputs and 4 outputs), either individually or synchronously. Each connection pair is equipped with a standalone pressure regulator and an analogue pressure gauge.
The trolley can be provided in a completely stand-alone version with its own dedicated control panel, so that it can be used not only with the spotting press.
Upon the customer’s request, it is possible to configure the marks of the moulds with the spotting press, in order to test the correct functioning of the sensors and of the hydraulic cylinders. We can supply special cycles for the movement of slides/hydraulic cylinders.
The standard trolley is equipped with a pump with a delivery of 8 Liters/min. and a 2.2 kW engine. A customized trolley version is characterized by a pump with a delivery of 40 liters/min. and 11/15 kW engine. A special version for operation with water-glycol mix is also available.
TECHNICAL ASSISTANCE
Diagnostic system
Integrated diagnostic system
MILLUTENSIL die & mould spotting presses are equipped with a specific and exclusive diagnostic program. Any failures occurred during operations is displayed on the control display, where the affected point is indicated. As a consequence, the machine downtime is minimized.
Main advantages:
- Minimization of down time,
- Quick and easy troubleshooting,
- Considerable service costs reduction, especially after the warranty period.
E-Won modem
MIL-Series spotting presses are equipped with a E-Won modem, so that our Millutensil technicians can remotely operate on the spotting press to fix it.
The remote assistance can be easily performed thanks to the hotspot of a mobile phone and a password that is provided in case of need.
Wireless mobile panel
Thanks to the tablet Siemens multitouch ITP 1000 (optional) and its MyMILL© App (optional), remote assistance is simplified, since the tablet can be used to initiate the remote assistance call.
Training
For a complete use of the machine, we provide support and training to technicians during installation on site.
TECHNICAL DATA
Description | MIL409 | ||
– Size of press plates | mm | 4000 x 4000 | |
– Max. clamping force | kN | 4000 | |
– Max. increased clamping force | kN | 5000 | |
– Max. opening force | kN | 1500 | |
– Max. load capacity on lower plate | kg | 160000 | |
– Max. load capacity on upper plate | kg | 60000 | |
– Min. – max. opening between plates
– Vertical stroke: 180° pit version |
mm | 500 – 4300 3800 | |
– Distance between columns | mm | 4654 | |
– T slots in the press plates for mould clamping | DIN.650 | T.28 | |
– Ø of centring hole in lower plate | mm | Ø 260 | |
– Ø of centring hole in upper plate | mm | Ø 260 | |
– High down stroke speed | mm/sec | 65-80 | |
– Slow down stroke working speed | mm/sec | 8 | |
– Power of main motor | kW | 45 | |
– Electrical connection | V / Hz | 440 / 60 | |
– Machine weight | kg~ | 170000* |
* further dimensions and weight capacities on demand
Our worldwide references
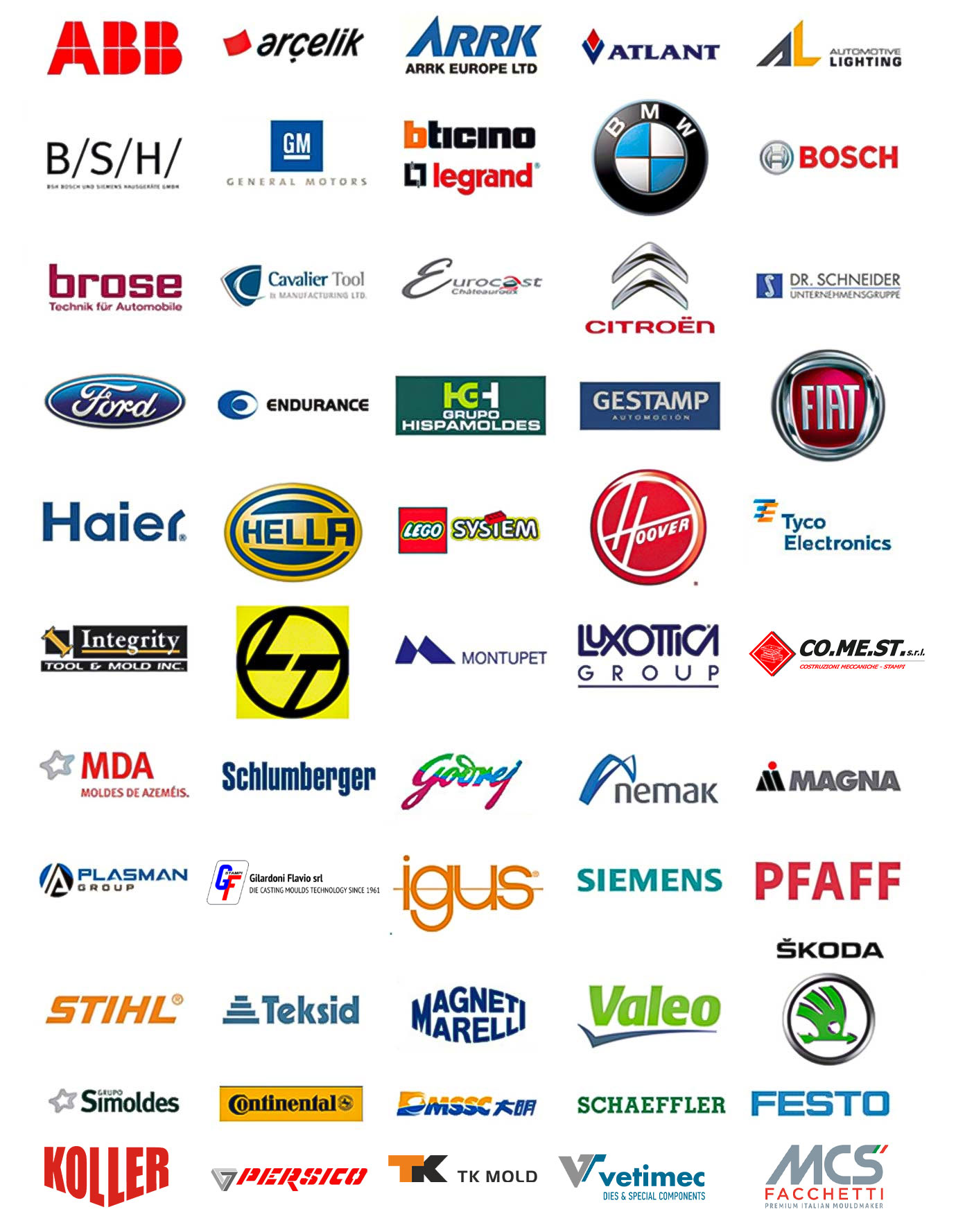