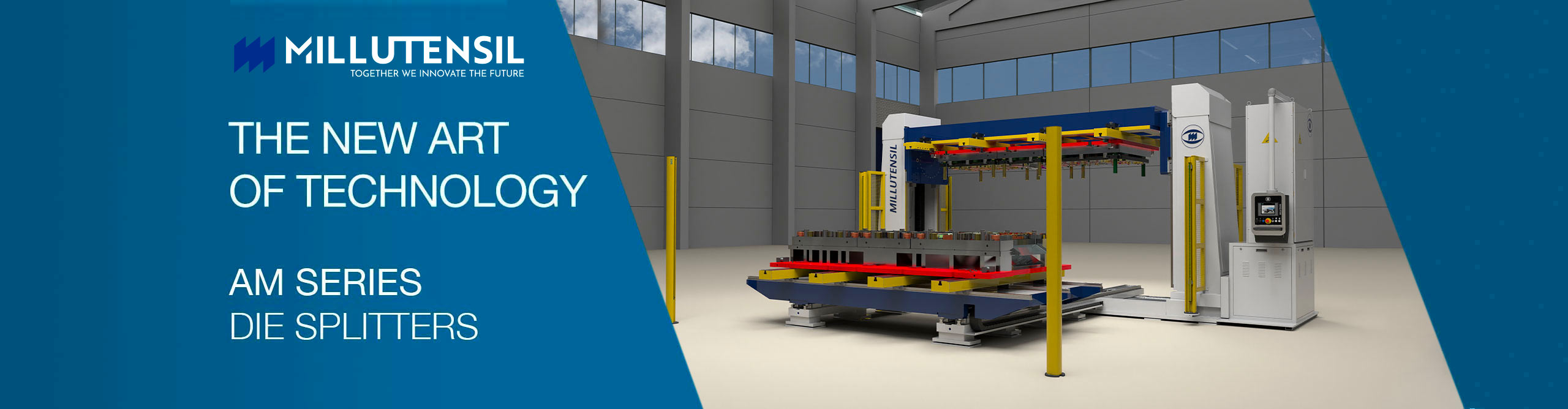
SOLUTIONS FOR ASSEMBLY, ADJUSTMENT, CHECKING AND REPAIR OF LARGE DIES
AM SERIES
At the forefront of innovation, MILLUTENSIL presents the die-splitter, a groundbreaking solution meticulously crafted to meet the evolving needs of our customers. Specifically designed to effortlessly manage large molds, the die-splitter extends its proficiency even into the sheet metal sector.
This cutting-edge equipment stands out as an innovative, versatile, and highly efficient solution, perfectly aligning with the escalating trend towards automation in manufacturing processes and the ever-increasing safety standards.
Key Advantages of the AM Series:
- Significant Reduction in Assembly and Maintenance Time: The AM series introduces a revolutionary approach, substantially minimizing the time and effort required for assembly and maintenance.
- Ergonomic Work Positions: Offering ergonomic work positions, the die-splitter ensures a comfortable and efficient environment for working on dies, enhancing overall productivity.
- Seamless Die Handling: Designed for ease of use, the die-splitter streamlines the process of handling dies, providing an exceptionally straightforward and efficient experience.
AMS 1530 | AMS 2030| AMS 3525 | AMS 3040 | AMS 5045
Die-splitter used for assembly, adjustment, checking and repair of dies for blanking, die casting, etc. with a very stable structure made of welded and normalized steel.
All components are purchased from well-known manufacturers, such as for example: hydraulic system Bosch-Rexroth, Hawe; electrical system Siemens, Schneider Elektrik, Phoenix Contact, Weidmüller. This guarantees a general good functionality of the die-splitter, and a quick procurement all over the world.
EC Declaration of Conformity and compliance with safety provisions in accordance with the current EC standards.
Click and drag to rotate the view. Scroll to zoom.
mold fixing
Millutensil die-splitters are designed to easily adapt to any mold shape and size.
STANDARD PLATEN MOVEMENTS
The lower trucks smoothly glide on rails using ball-bearing rollers with hydraulic drive.
This motion facilitates the extension of the lower mold section beyond the columns in an easily accessible position for the work outside the die-splitter.
The upper brackets vertically slide, driven by electronically controlled parallel-axis ball screw mechanisms.
Upon reaching the highest position, they can be rotated forward by 180° and subsequently lowered to the ground to achieve a comfortable working position.
Clamping in the exact horizontal position is ensured by four hydraulically actuated locating pins.
In the final position, the two mold halves are aligned. This means an advantageous working position, and at the same time maximum working safety facilitating the swift assembly and disassembly of various mold parts
All movable parts effortlessly glide on ball-bearing roller guides.
OPTIONAL PLATEN MOVEMENTS
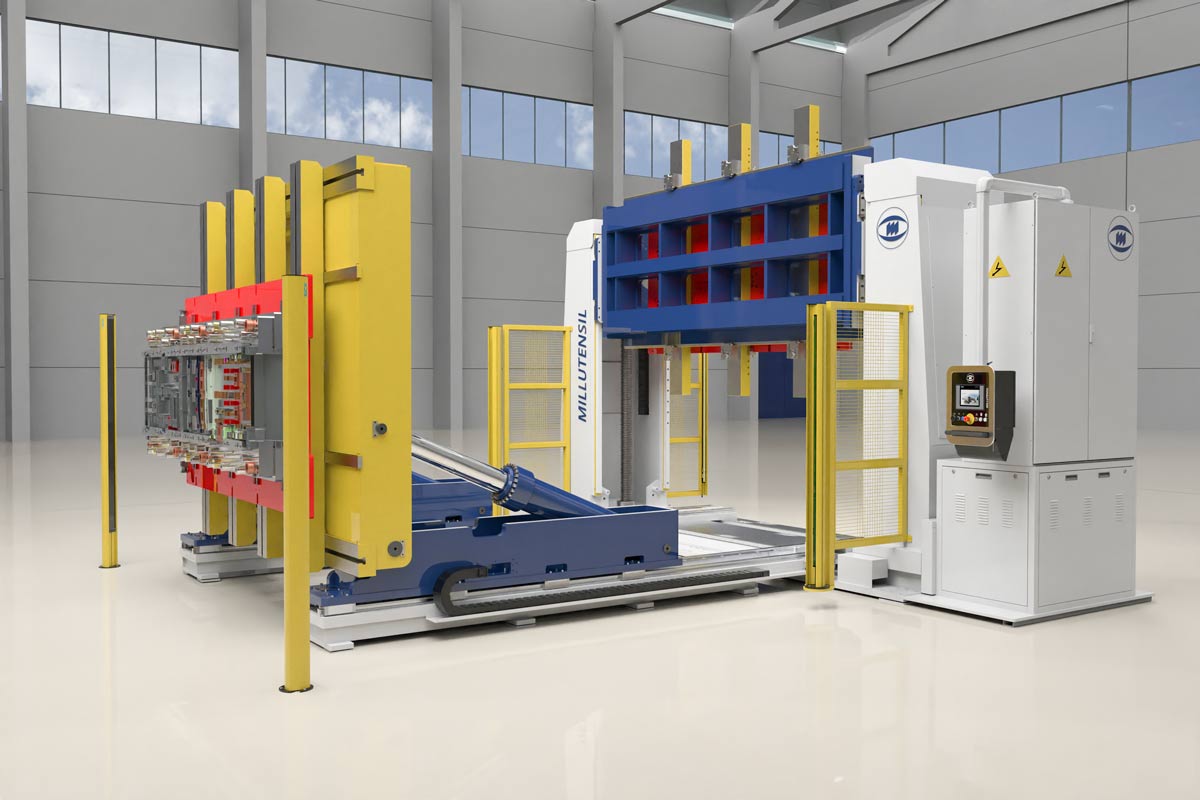
Optionally, the lower plane can be tilted by 90°.
This facilitates intervention operations on the mold, allowing the operator to maintain an upright posture. However, the load capacity of the lower plate decreases by approximately 30%.
SPECIAL VERSION AMS
This optional version involves motorizing the clamping bars for the lower and upper die plates. This functionality is made possible by employing two independent lower trucks that adjust to the width of the mold, sliding on ball-bearing rollers with hydraulic drive, and two hydraulically motorized upper sliding brackets that adjust to the depth of the mold.
Click and drag to rotate the view. Scroll to zoom.
mold fixing
Millutensil die-splitters are designed to easily adapt to any mold shape and size.
The lower half of the mold is fixed on independent trucks that adjust to the width of the mold, sliding on ball guide rollers with hydraulic drive.
The upper half of the mold is fixed on sliding brackets that accommodate the mold’s depth.
PLATEN MOVEMENTS
The lower trucks smoothly glide on rails using ball-bearing rollers with hydraulic drive.
This motion facilitates the extension of the lower mold section beyond the columns in an easily accessible position for the work outside the die-splitter.
The upper brackets vertically slide, driven by electronically controlled parallel-axis ball screw mechanisms.
Upon reaching the highest position, they can be rotated forward by 180° and subsequently lowered to the ground to achieve a comfortable working position.
Clamping in the exact horizontal position is ensured by four hydraulically actuated locating pins.
In the final position, the two mold halves are aligned. This means an advantageous working position, and at the same time maximum working safety facilitating the swift assembly and disassembly of various mold parts
All movable parts effortlessly glide on ball-bearing roller guides.
VIDEO
FEATURES
Structure
- Die-splitter with 2 chrome-plated, alloy steel uprights, structures made of welded and normalized steel, and a sturdy cast iron baseplate to guarantee high rigidity and bending resistance.
- All movements are carried out by means of recirculating ball slides on high precision guides.
- Basement embedded in a robust arc-welded structure, that is highly rigid and flexion-proof
CONTROL PANEL
TOUCH PANEL FOR AMS SERIES
Uncluttered, clear and ergonomic, the panel offers many advantages as well as vast flexibility in customizing features.
Siemens S7-1500 control easy to program and use.
The control panel is equipped with a touch panel with user-friendly graphics to simplify the use of the die-splitter. Due to security reasons, some functions can be activated only through traditional buttons (i.e. the downstroke has to be performed with two-hands in accordance to the EU safety legislation).
The control panel is mounted suspended on the die-splitter right side and can also be rotated to the back so that it is even easier to use for the operator.
Two-hands command.
Due to security reasons, some functions can be activated only through traditional buttons (i.e. downstroke must be carried out with two-hands, in compliance with EU-UL-CSA safety legislation).
In the pulpit station a new Siemens multi-touch ITP 1000 can be embedded (OPTIONAL).
This new Siemens multi-touch ITP 1000 is supported by a dedicated app called MyMILL© App, that has been developed by Millutensil as a result of the ongoing cooperation between Millutensil and their customers.
EQUIPMENTS FOR THE DIE-SPLITTERS
ELECTRONIC UPPER PLATE PARALLELISM ANTI-UNBALANCE SAFETY DEVICE
ELECTRONIC MANAGEMENT OF AM DIE-SPLITTERS’ UPPER PLATE MOVEMENTS
The AMS series die-splitters are equipped with advanced electronic control to manage the upward and downward movements of the upper plate. Furthermore, a cutting-edge safety device for monitoring and managing the parallelism of the upper plate ensures precision and safety in operations.
The independent upper supports, sliding vertically, are activated through recirculating ball screws powered by efficient brushless motors. Electronic height monitoring, facilitated by these motors, allows real-time control of the upper plane’s parallelism, with values conveniently displayed on the control panel. In case the pre-established limit parameters are exceeded, the closing movement of the ram is immediately deactivated, and the parallelism condition is automatically restored through the ascent function.
Emphasizing the crucial role in maintaining impeccable parallelism between mold planes, this electronic precision becomes the cornerstone to ensure optimal performance, durability, and extended lifespan of the mold opener.
With this particular system, we can manage specific predefined positions, adjustable and memorizable for each mold. This allows for the automatic application of different speeds, benefiting repeatability and safety. The device comprehensively manages the synchronized movement of the two geared motors for the ascent and descent that move the upper plane of the mold opener.
The use of this system protects both the die-splitter and the molds themselves from potential damage.
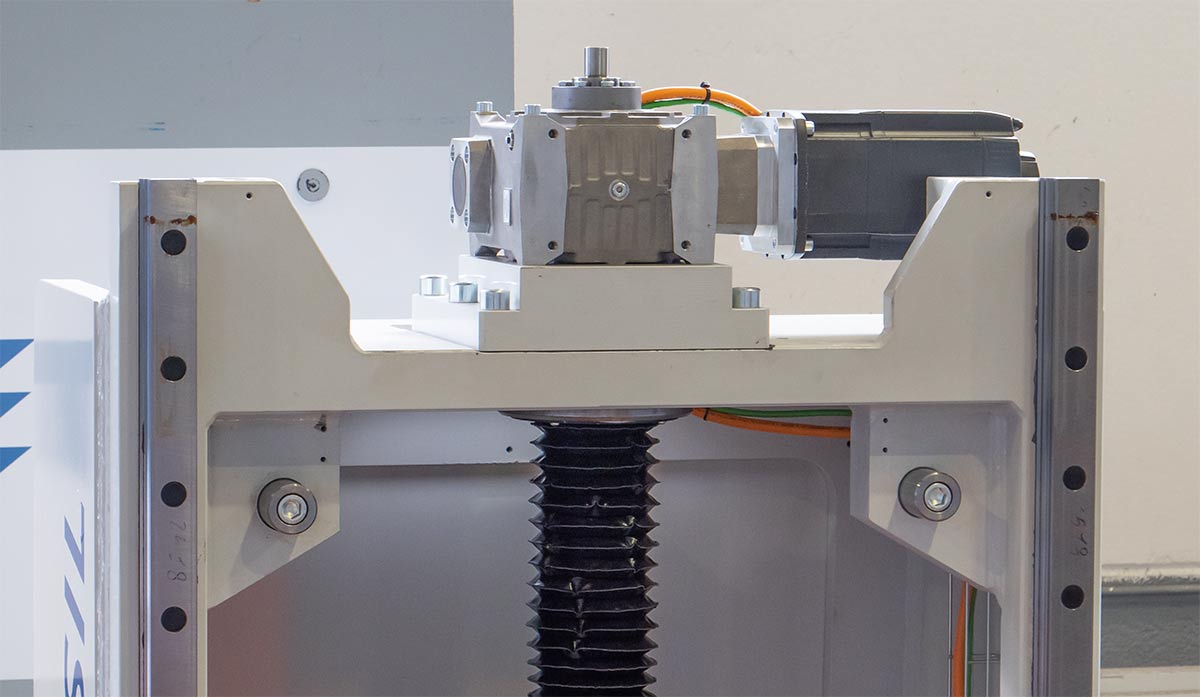
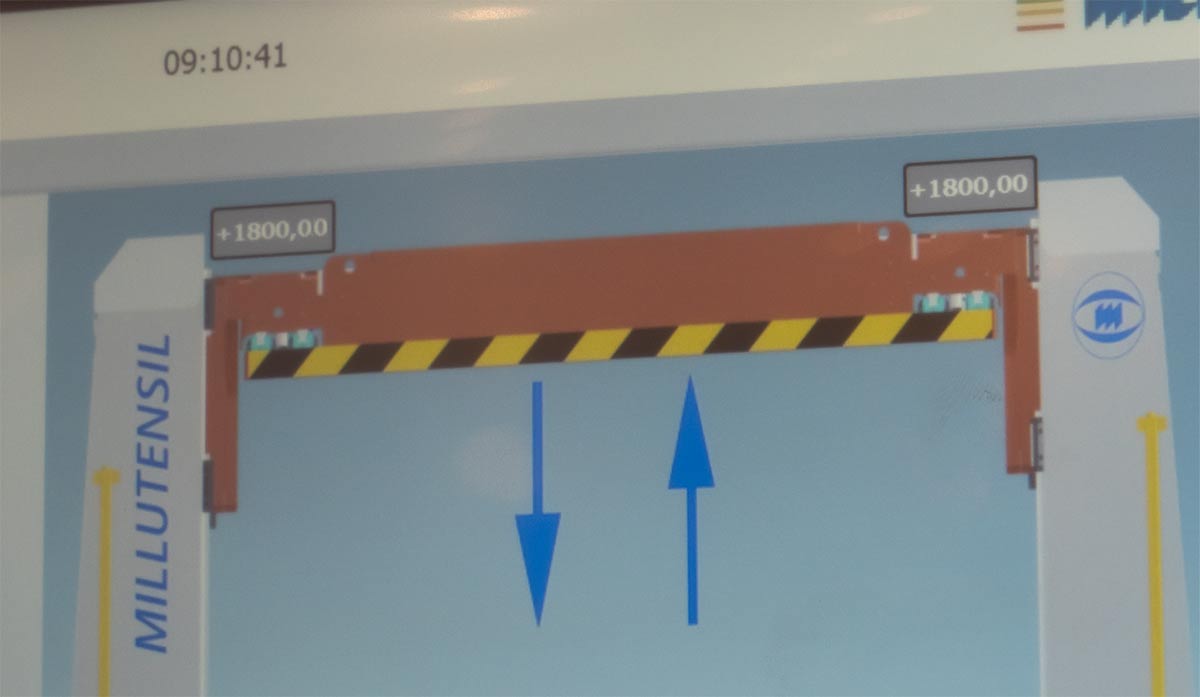
ELECTRICAL CABINET
The electrical panel of MILLUTENSIL die-splitters is ingeniously integrated into a dedicated cabinet seamlessly positioned on the right side of the die-splitter. Importantly, this cabinet is not an external entity but an integral part of the press itself. This strategic integration eliminates the need for external electrical cables, contributing to a cleaner and more organized workspace.
Beyond aesthetics, this design choice enhances accessibility, ensuring that there are no extraneous cables obstructing the machine’s functionality. The absence of external junction cables not only improves the overall cleanliness of the setup but also streamlines access to the press, simplifying maintenance procedures and underlining our commitment to delivering a cutting-edge and user-friendly solution.
All electrical boards and cards, supplied mainly by SIEMENS, are safe in compliance with CE, UL, CSA standards.
LIGHT CURTAINS: ACCIDENT-PREVENTION PROTECTION DEVICES
The safety of the operator is meticulously ensured through the deployment of optional protective devices featuring light barriers strategically positioned in areas that may be partially obscured from the operator’s line of sight.
Should you be interested in further enhancing operator safety, Millutensil offers the option to equip your system with these advanced safety features. This comprehensive safety system comprises light barriers that can be activated and monitored by a dedicated safety module, under the precise control of the PLC.
These measures underscore Millutensil’s unwavering commitment to workplace safety, offering advanced technologies and systematic safety protocols a features to further safeguard the well-being of operators during operational processes.
green mode
Utilizing a specialized low-pressure circuit, Millutensil employs an innovative approach to oil management. Through this system, oil is efficiently drawn from the tank, facilitating higher operational speeds without inducing oil heating, thus ensuring a significantly reduced energy consumption.
In line with our commitment to environmental stewardship, we have incorporated features that prioritize energy efficiency. For instance, after 100 seconds of inactivity, the hydraulic unit intelligently powers down to conserve energy resources. This strategic energy-saving measure aligns with Millutensil’s dedication to sustainability and environmental responsibility.
For swift reactivation, a simple press of the dedicated push-button promptly restores hydraulic pressure, combining operational efficiency with conscientious energy management practices. This dual focus on performance and environmental sustainability underscores Millutensil’s pledge to deliver cutting-edge solutions that prioritize both productivity and eco-consciousness.
OPTIONAL EQUIPMENTS FOR THE DIES
DIE HOLDING BEAMS WITH HYDRAULIC BALL INSERTS
The trucks of lower plate are equipped with hydraulic ball inserts that play a crucial role in the die assembly and disassembly process.
Specifically, these beams are designed to facilitate the manual centering and coupling of the two halves of the dies after potential disassembly. When the dies need to be separated, the hydraulic ball inserts streamline the process, allowing for efficient realignment and coupling when it’s time to reassemble. This feature enhances the user’s ability to manage the dies manually, ensuring precision and ease during both disassembly and assembly phases of the die-splitter operation.
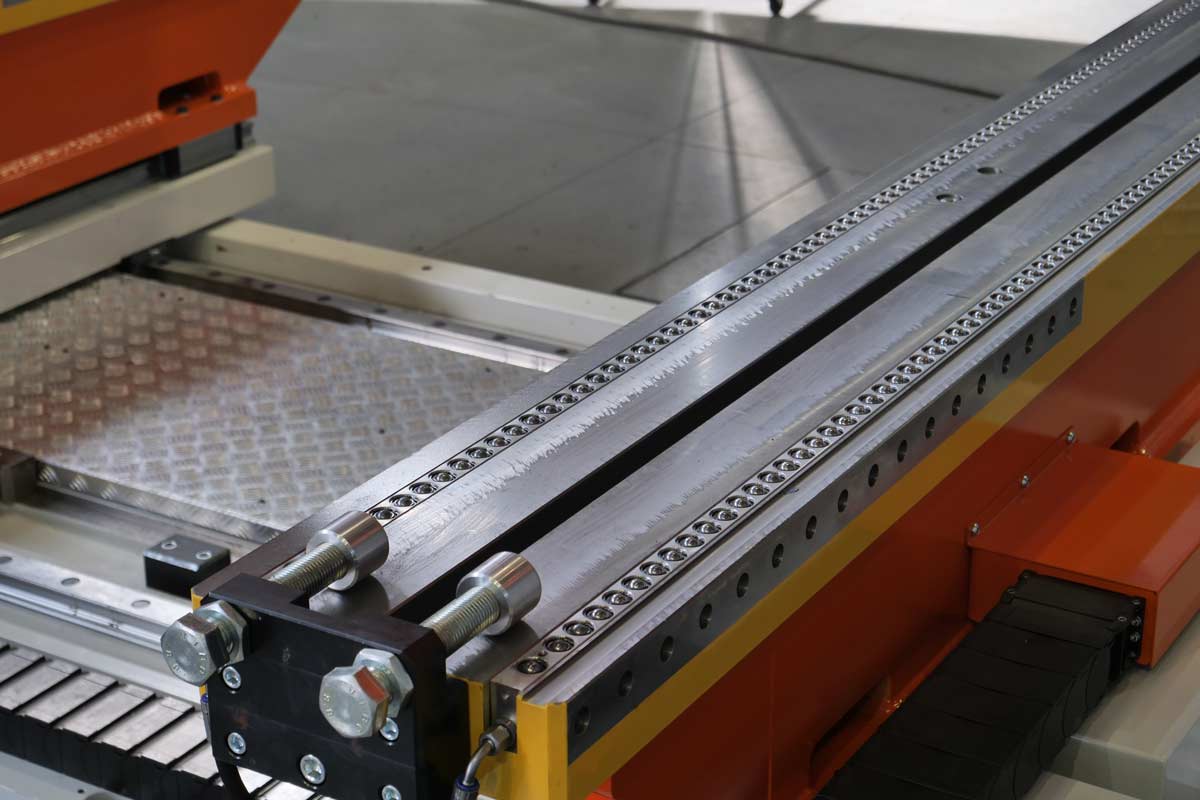
CENTERING BLOKS
Centering blocks are mechanical components employed in situations where only one half of the mold is disassembled for maintenance purposes. These blocks serve as essential references to ensure the accurate recentering of the other half of the mold during the reassembly process.
When maintenance requires the separation of only one part of the mold, the centering blocks come into play. These blocks provide precise points of alignment, allowing for the seamless and accurate realignment of the remaining mold half. Their role is crucial in maintaining the overall integrity and precision of the mold assembly, contributing to the efficiency and effectiveness of the maintenance procedure.
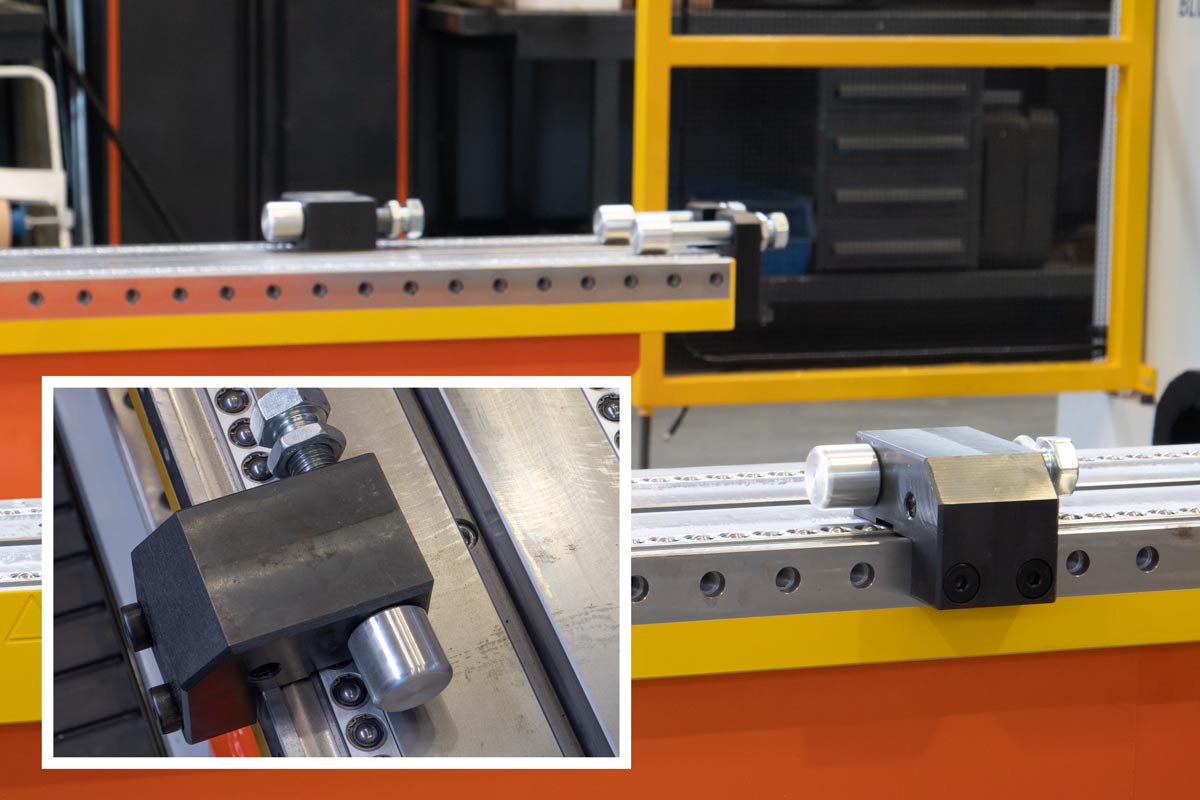
TECHNICAL ASSISTANCE
Diagnostic system
Integrated diagnostic system
MILLUTENSIL die-splitters are equipped with a specific and exclusive diagnostic program. Any failures occurred during operations is displayed on the control display, where the affected point is indicated. As a consequence, the machine downtime is minimized.
Main advantages:
- Minimization of down time,
- Quick and easy troubleshooting,
- Considerable service costs reduction, especially after the warranty period.
E-Won modem
MILLUTENSIL die-splitters are equipped with a E-Won modem, so that our Millutensil technicians can remotely operate on the die-splitter to fix it.
The remote assistance can be easily performed thanks to the hotspot of a mobile phone and a password that is provided in case of need.
Wireless mobile panel
Thanks to the tablet Siemens multitouch ITP 1000 (optional) and its MyMILL© App (optional), remote assistance is simplified, since the tablet can be used to initiate the remote assistance call.
Training
For a complete use of the machine, we provide support and training to technicians during installation on site.
OPTION ON DEMAND
TECHNICAL DATA
Description | AMS1530 | AMS 2030 | AMS 3525 | AM 3040 | AM 5045 | |
– Size of press plates | mm | 3000 x 1700 | 3000 x 2200 | 3500 x 2500 | 4000×2000 | 4500×2800 |
– Min opening between plates | mm | 320 | 300 | 300 | 500 | 500 |
– Max opening between plates | mm | 1450 | 1800 | 1800 | 2100 | 2200 |
– Max. load capacity on lower plate | kg | 15000 | 25000 | 30000 | 30000 | 50000 |
– Max. load capacity on upper plate | kg | 7000 | 11000 | 15000 | 13000 | 20000 |
Our worldwide references
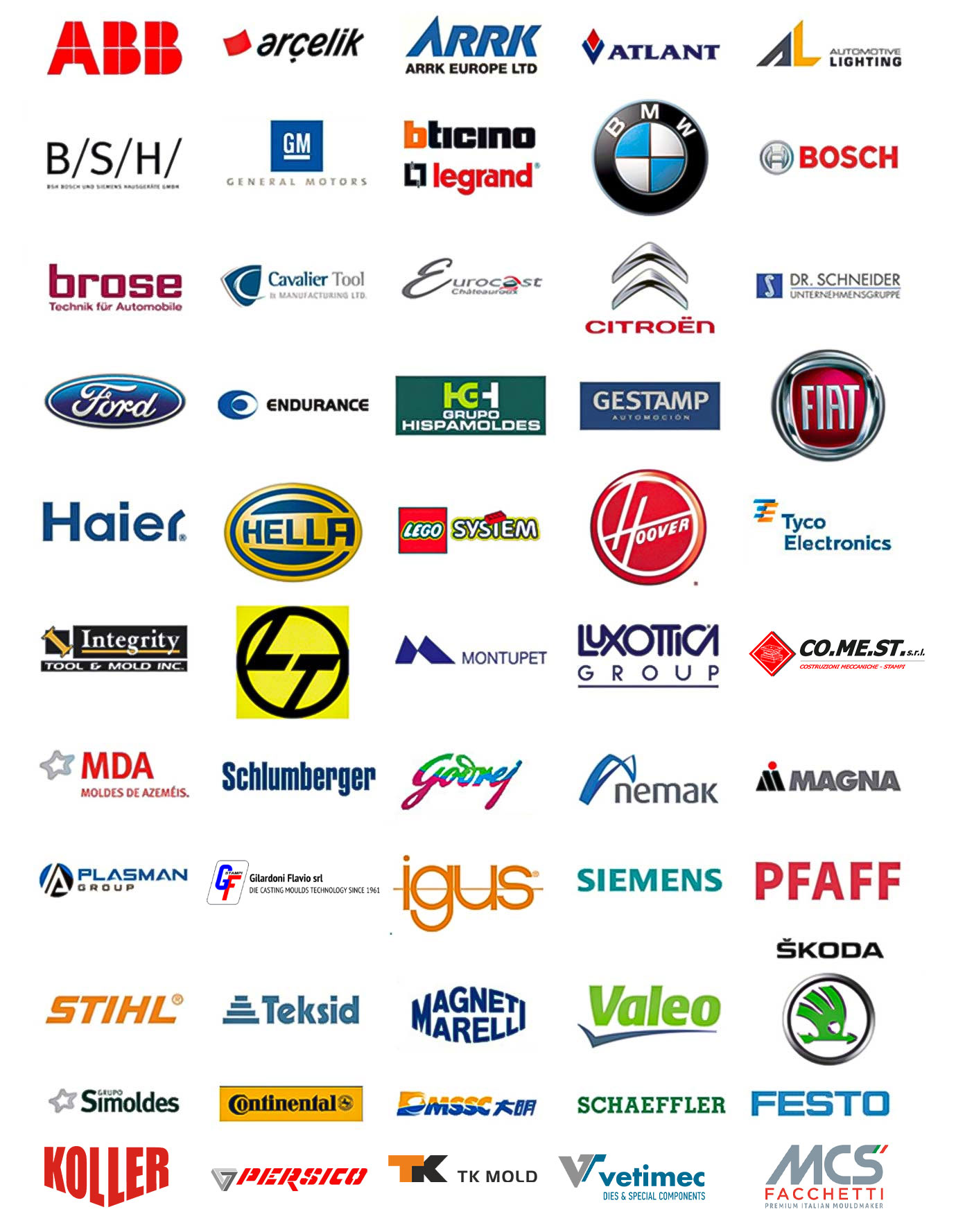